en-us-Análisis estructural limitador soporte de motor
Hoy vamos a presentar un análisis estructural de un limitador de chapa estampada, similar a los encontrados en los soportes de motor de vehículos automotores.
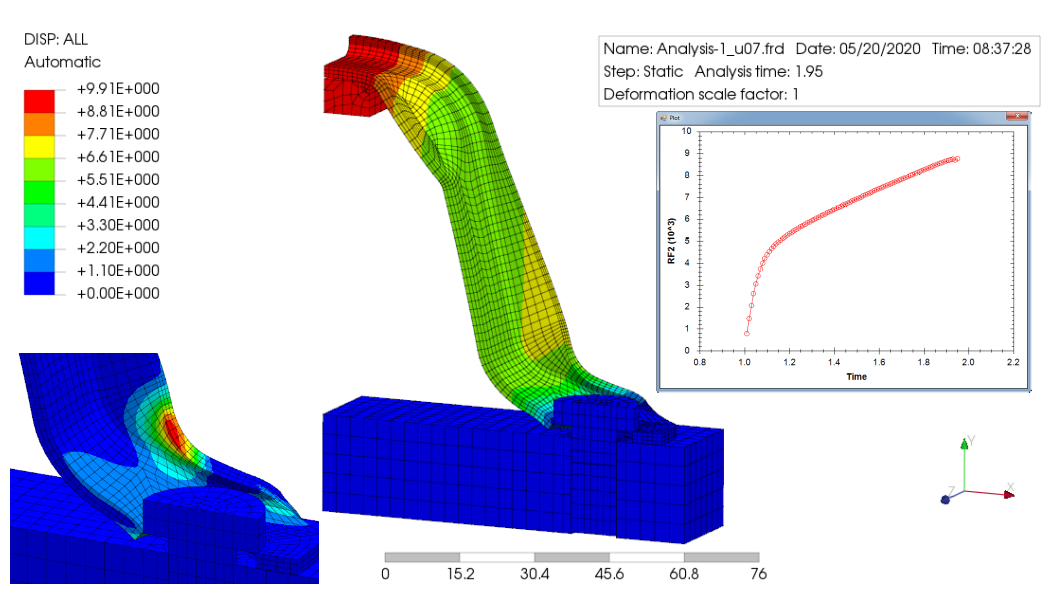
Estas piezas pueden ser fabricadas en aluminio, fundición (camionetas), plástico reforzado con fibra de vidrio (vehículos de alta gama) o chapa estampada como en el caso que analizaremos en este artículo.
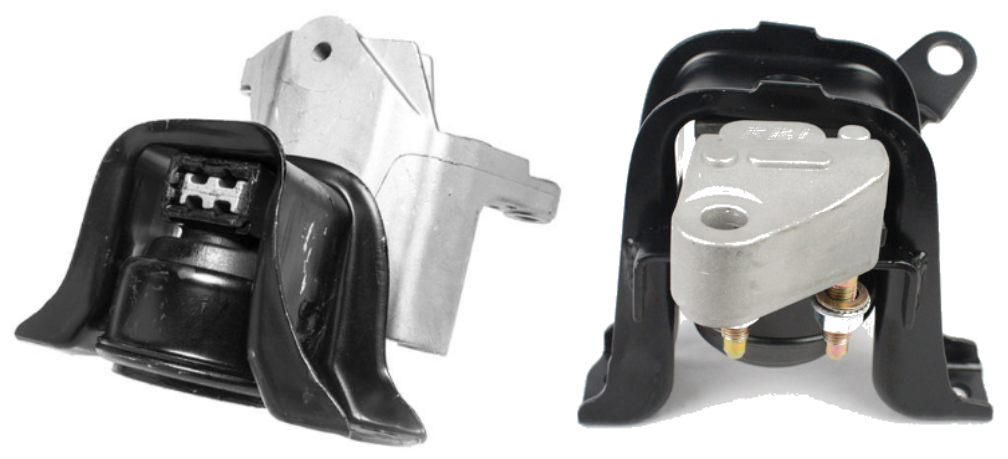
El limitador cumple dos funciones principales, permitir fijar el soporte de motor a la carrocería, y limitar los movimientos del motor ante distintos casos y direcciones de carga:
- Esfuerzos verticales: Cuando pasamos por un pozo, la carrocería baja, pero por inercia el motor intenta mantenerse en posición, causando una fuerza vertical sobre la cara interior del limitador. A la inversa, cuando pasamos por un lomo de burro, la carrocería sube, el motor intenta quedarse en la misma posición produciendo una fuerza sobre la cara inferior de la carrocería.
- Esfuerzos longitudinales: Con las aceleraciones o frenadas bruscas, o impactos frontales/traseros, el motor intenta conservar su posición de equilibrio, provocando esfuerzos sobre las caras verticales del limitador.
- Esfuerzos laterales: Producidos por las dobladas bruscas o impactos laterales, estos esfuerzos son tomados por el soporte de caja en esta configuración de soportes (soporte motor, soporte caja y restrictor de torque)
El limitador tiene que ser capaz de soportar todos estos esfuerzos, por lo que durante su diseño debe ser validado con herramientas de FEA, y luego obviamente ensayado físicamente en banco de pruebas y en vehículo.
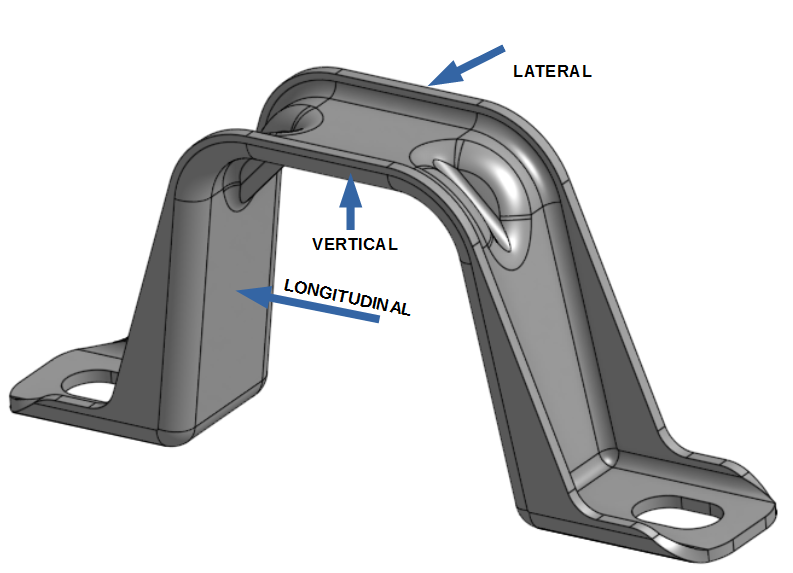
El modelado de la pieza fue realizado en Onshape, una poderosa herramienta de CAD online. Se utilizaron operaciones de superficie, luego fue aplicado el espesor y simetrías para obtener el modelo final. En la siguiente animación se muestran las operaciones para conseguir la geometría final.
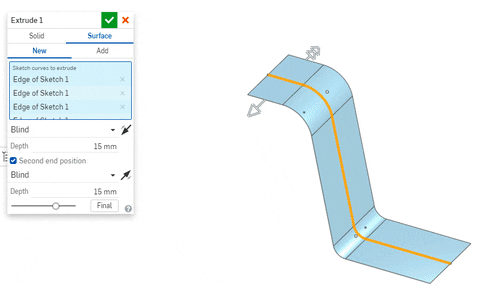
Una vez modelada, la pieza es exportada a Salome para su mallado. Se realizó un mallado mapeado con elementos del tipo quad, que luego fue extrudado para obtener una malla de hexaedros con tres elementos en el espesor. En la animación pueden observarse las particiones y secuencia de mallado del componente.
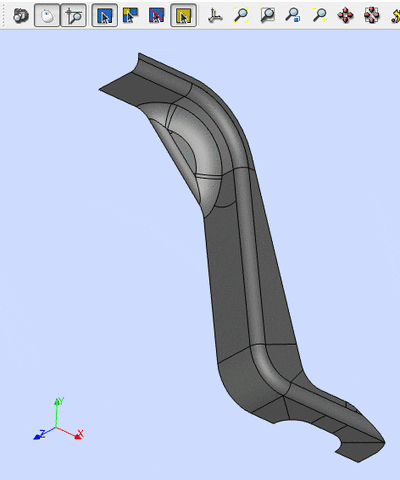