Simulación de
Recipientes bajo presion / Válvulas

La simulación de recipientes a presión es una herramienta útil y esencial que permite al ingeniero estudiar su comportamiento y conocer, si bajo los posibles escenarios de operación, el diseño provisto garantiza un desempeño óptimo.
Predecir el desempeño de recipientes a presión puede ser útil, por ejemplo, para la localización de posibles lugares de falla durante distintas etapas en la operatoria de un proceso industrial, como también para la optimización del diseño. Conozca los servicios que 4P Ingeniería puede ofrecer:
Mallados
Todo buen análisis exige una malla adecuada. Las características geométricas de los recipientes de presión exigen mallar con elementos hexaédricos, de forma de poder tener al menos tres elementos en el espesor de las paredes delgadas. En caso de casquetes fabricados por embutido, es recomendable trabajar con elementos de cascara (shell) para poder tomar en cuenta cambios de espesor debido al proceso de embutido.
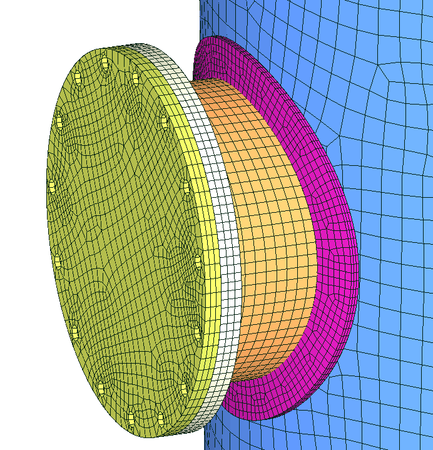
Materiales
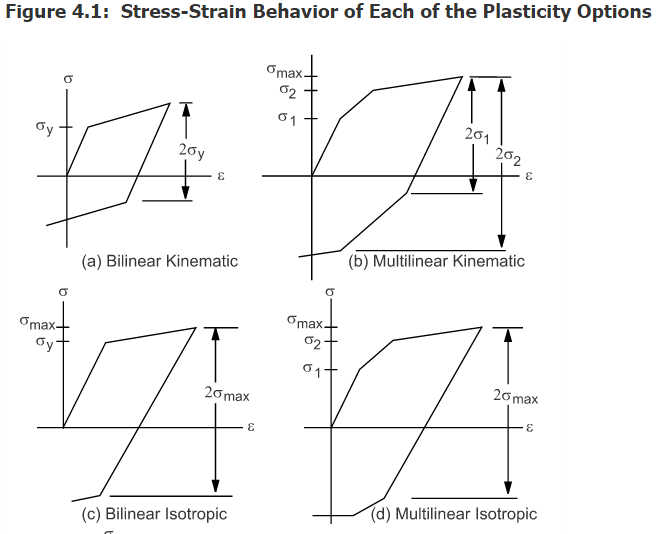
Si existe la necesidad de calcular deformaciones permanentes, diferentes comportamientos no lineales pueden ser incorporados al modelo. Diferentes materiales y calidades pueden ser representados con precisión.
Condiciones de borde
Presiones, fuerzas, contactos, todas pueden ser incoporadas al modelo, ya sea en forma instantánea o variables en el tiempo (no lineales)
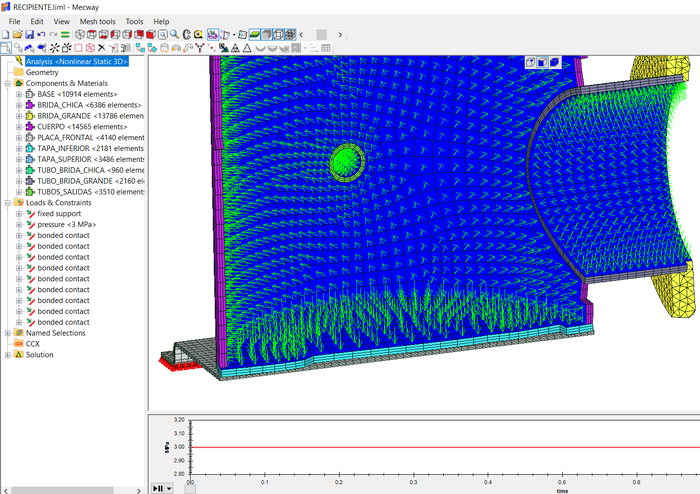
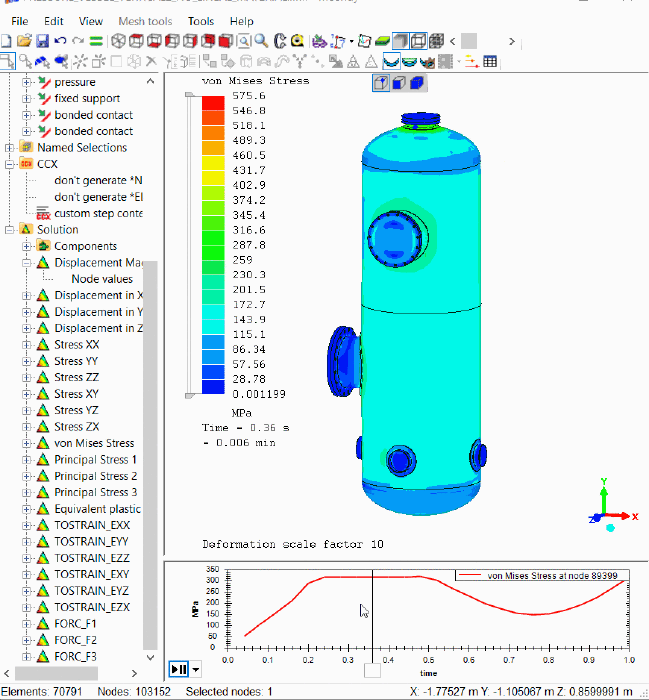
Análisis de Tensiones
Sólo un análisis no lineal puede mostrarle donde las tensiones pueden superar el límite elástico dando lugar a fallas por deformaciones plásticas en el modelo.
Deformaciones
En un análisis no lineal el recipiente puede quedar deformado plásticamente luego de liberar la carga. Conozca cuanto y donde queda deformado fácilmente
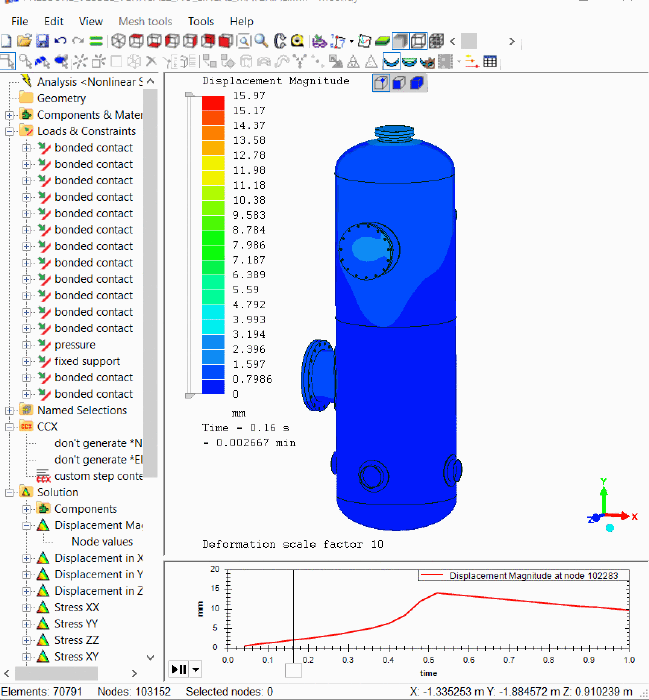
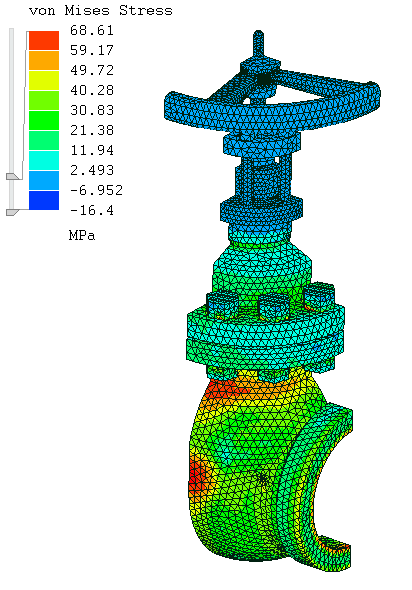
Válvulas
El diseño de cuerpos de válvulas de formas complejas, no responde a procedimientos simples de cálculo. Si bien los códigos de diseño, (por ejemplo ASME B16.34, 2004) establecen el espesor requerido del cuerpo o carcasa de las válvulas, aquellas de formas complejas, gran tamaño y/o sometidas a elevadas presiones (serie 600 y mayores), requieren de un estudio más riguroso y detallado, para asegurar su integridad. Es importante entonces, realizar un análisis previo a la prueba hidrostatica, que permita su optimizacion, para evitar perjuicios económicos a sus fabricantes por deficiencias en los diseños.
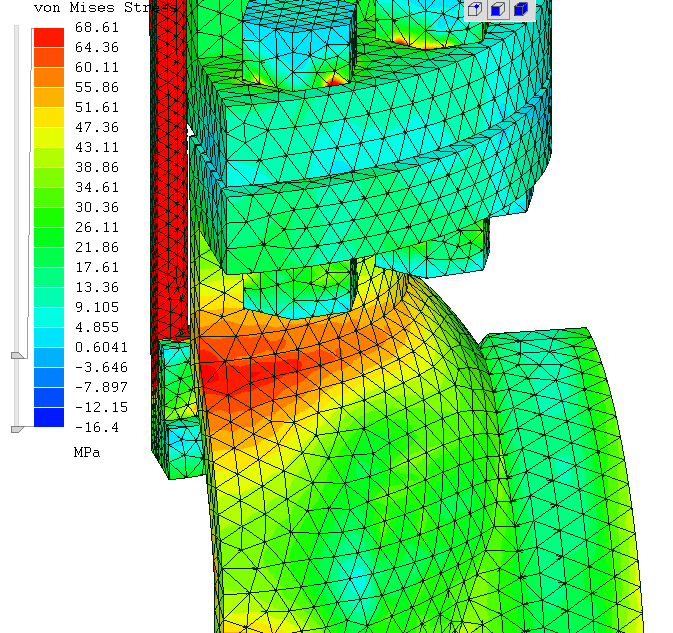
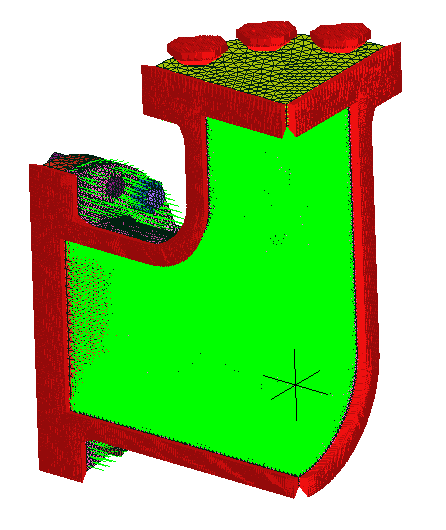
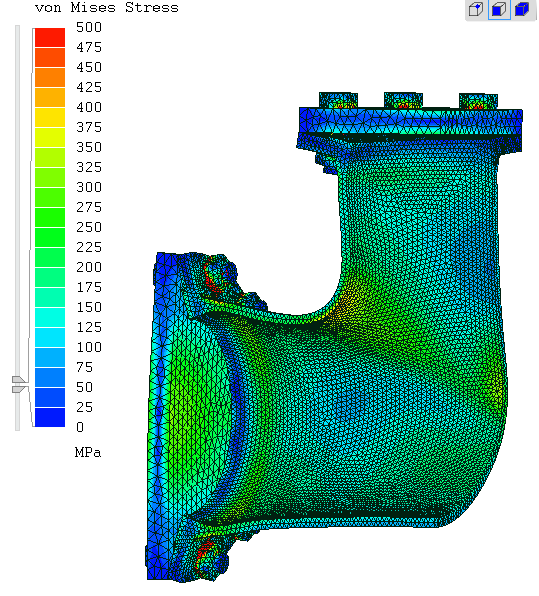